- Laminated Busbar
- Film Capacitor
- Film Capacitor for HEV / EV Motor Control Unit
- DC-Link Capacitor ( Dry-Type, Plastic Case, Maximum Temperature 85℃)
- DC-Link Capacitor ( Dry-Type, Plastic Case, Maximum Temperature 105℃)
- MKP DC-Link Film Capacitor
- Water Cooled Heat Sink
- Flat Heat Pipe
- Reactor
- Water Cooling Reactor
- Input AC Reactor
- Output AC Reactor
- DC Reactor
- Reactor for Explosion-Proof Inverter
- Sine Wave Filter
- Detuned Reactor
- DV/DT Filters
- Three-Phase Input Filter
- Resistor
- Wirewound Resistor
- Aluminum Enclosure Resistor
- Aluminum Housed Resistor
- Die-Casting Aluminum Resistor
- Aluminium Resistor (Multiple Unit)
- Thick Film Resistor
- Braking Resistor Box
- Wirewound Tubular Fixed Resistor
- Power Resistor Unit
- Crowbar Resistor
- Braking Unit
Water Cooled Heat Sink
Product Profile
The power components such as IGBT, GTO, etc., are employed in this water cooled heat sink which is a type of highly efficient radiator. It is used for controlling the temperature of the power module so that the temperature under the working environment would not exceed the highest temperature specified by the regulation and standard. The calculation of the maximum permissible temperature is based on the finite element thermal analysis and the working condition analysis of the components of this water cooled heat sink. Besides, the calculation should be in conformity with the requirements for the reliability and the service environment of this water cooled heat sink. In this way, the safety and reliable, steady operation of the power module as well as a longer service life of the equipment can be guaranteed.
Dimension | Length×Width×Thickness: < 1250×800×60mm |
Superficial treatment | Wash, Black anodized, Nickel plating |
Chrome plating | |
Planeness | <0.05(100×100) |
Roughness | <1.6μm |
Connection Type | Vacuum brazing or argon arc welding |
Coolant temperature (℃) | Minus 30℃ to minus 60℃ |
Coolant | Pure water or the mixed liquid of water and glycol |
Flow (LPM) | <80L/min |
Surface temperature rise (℃) | <30℃ |
Max. working pressure (kPa) | 0.6Mpa-3.0MPa |
Calorific value | <30kW |
Thermal resistance | <2℃/kw (depends on the heat source distribution) |
Structure | Process | Feature | Photo |
Drilling type | Bend the copper pipe or stainless steel pipe, embed the water pipe CNC profile processing |
Simple process, low cost in volume production and poor performance | ![]() |
Pressure tube type | Milling groove or section bar slot broaching to embed the bended copper pipe into the slot by welding, pressing and pasting. CNC profile processing | Simple technology, low cost in volume production and poor performance | ![]() |
Assembling type | CNC or die-casting water chamber, body shape and cover. Seal by using the screw and seal ring or glue | Simple process, low cost, medium performance and low reliability | ![]() |
Friction welding/ Electron beam welding | Use the CNC to process the water chamber and cover. Conduct the seal welding by the friction welding or electron beam welding. CNC process the finished products. | Relatively complicated process, flexible structure and good performance, high reliability and Relatively high cost | ![]() |
Vacuum brazing | Process the water chamber by using CNC or other ways. Conduct the face seal via the vacuum brazing. Process the finished products by way of CNC. |
complicated process, flexible structure, best performance, high reliability and the highest cost |
![]() |
LCP Properties & Parameters of FZ450R12ME3
Liquid cooling plate is adaptable for all thermal devices with the size of 62mm×122mm. The ΔT of LCP = thermal resistance × heat dissipation power.
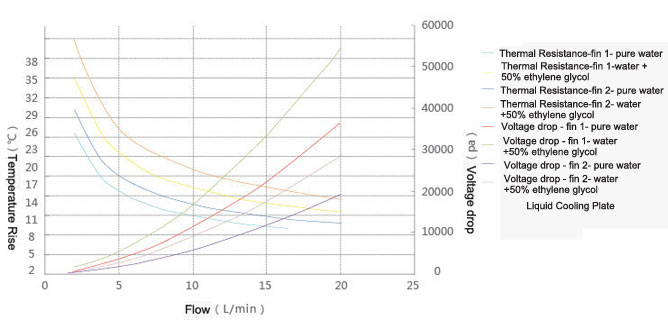
Fin A (3mm in height) | |||
Pure Water | (pure water) | 50% pure water +50% ethylene glycol | |
Flow rate, L/min |
Heat Resistance (R,℃/kw) |
Pressure Drop (ΔP, Pa) |
Heat Resistance (R,℃/kw) |
2 | 23.4 | 752 | 32.3 |
4 | 16.3 | 2375 | 22.8 |
6 | 13.5 | 4727 | 18.9 |
8 | 11.9 | 7709 | 16.6 |
10 | 10.8 | 11267 | 15.1 |
12 | 10.1 | 15363 | 14 |
14 | 9.5 | 19968 | 13.2 |
16 | 9.1 | 25058 | 12.5 |
18 | 8.7 | 30616 | 11.9 |
20 | 8.4 | 36624 | 11.5 |
Fin B (5mm in height) | ||||
pure water | Pure water+50% glycol | |||
Pressure Drop (ΔP,Pa) |
Heat Resistance (R,℃/kw) |
Pressure Drop (ΔP,Pa) |
Heat Resistance (R,℃/kw) |
Pressure Drop (ΔP,Pa) |
1602 | 27.1 | 386 | 37.8 | 682 |
3971 | 19 | 1252 | 27 | 1904 |
7272 | 15.8 | 2495 | 22.5 | 3735 |
11613 | 13.9 | 4069 | 19.8 | 6078 |
16874 | 12.6 | 5947 | 18 | 8877 |
22961 | 11.8 | 8109 | 16.7 | 12102 |
29819 | 11.1 | 10540 | 15.7 | 15729 |
37408 | 10.5 | 13227 | 14.9 | 19738 |
45696 | 10.1 | 16161 | 14.2 | 24115 |
54658 | 9.7 | 19332 | 13.6 | 28847 |
Pressure distribution pattern
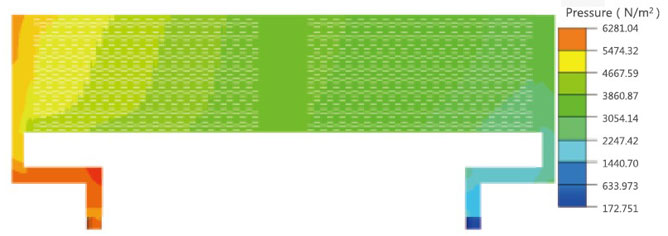
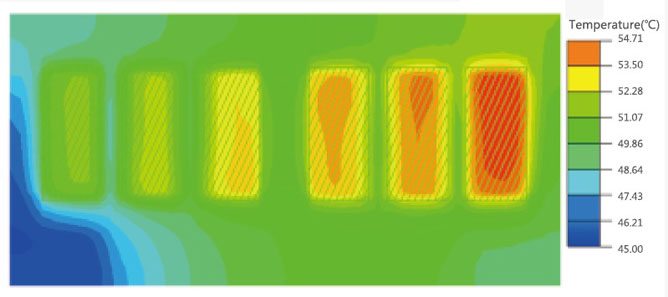
Range of Applications
1. Transportation: Electrical locomotive, railway, electric drive vessels, electric cars and so on.
2. Smart grid UHVDC, VSC-HVDC and so on.
3. New energy, wind power converters, photovoltaic power converters and so on.
4. Other industries such as frequency converter, signal processing, UPS, medical appliance, laser and so on.