- Laminated Busbar
- Film Capacitor
- Film Capacitor for HEV / EV Motor Control Unit
- DC-Link Capacitor ( Dry-Type, Plastic Case, Maximum Temperature 85℃)
- DC-Link Capacitor ( Dry-Type, Plastic Case, Maximum Temperature 105℃)
- MKP DC-Link Film Capacitor
- Water Cooled Heat Sink
- Flat Heat Pipe
- Reactor
- Water Cooling Reactor
- Input AC Reactor
- Output AC Reactor
- DC Reactor
- Reactor for Explosion-Proof Inverter
- Sine Wave Filter
- Detuned Reactor
- DV/DT Filters
- Three-Phase Input Filter
- Resistor
- Wirewound Resistor
- Aluminum Enclosure Resistor
- Aluminum Housed Resistor
- Die-Casting Aluminum Resistor
- Aluminium Resistor (Multiple Unit)
- Thick Film Resistor
- Braking Resistor Box
- Wirewound Tubular Fixed Resistor
- Power Resistor Unit
- Crowbar Resistor
- Braking Unit
Laminated Busbar
Product Profile
The laminated busbar is applied to connect the power devices of the electrical and electronic product. It reduces the distributed inductance of the circuit by means of the structural style of the lamination and parallel distribution of the anode and cathode. In this way, the voltage surge is reduced when the power component is turned off. Therefore, this product lowers the requirement for the voltage resistance of the power component, improves the reliability and stability of the operation of the component and meanwhile enhances the integration level of the current circuit. Last but not least, it is convenient for maintenance.
This laminated Busbar could be customized or specified according to your design or drawings. Clients can also provide information of real application information for us and we can design products on the basis of such information.
Features
1. Low inductance coefficient
2. Compact Structure and effective use of space and control of the system temperature
3. Minimal impedance and voltage drop
4. Strong overload capacity
5. Reduction of the harms caused by peak voltage to the components and extension of the service life of the electronic components
6. Reduction of the system noise and the electromagnetic interference/radio frequency interference
7. Easy installation and convenient on-site maintenance
8. Fewer components and improvement of the system reliability
9. Equally distributed capacitance
10. Simplicity and beauty in appearance
Item | Description |
Operating voltage range | 0~20kV |
Rated current range | 0~3600A |
Product structure | Hot pressing edge sealed, hot pressing edge open, hot pressing edge with potting |
Max. size | 1600×800mm |
Flame rating | UL94 V-0 |
Conductor material | T2 Cu 、 1060 AL |
Conductor surface treatment | Passivation, tin plated, nickel plated or silver plated |
Connection with the device | Embossing, riveted bronze columns, welded copper columns |
Insulation resistance | 20MΩ ~ ∞ |
Partial discharge | <10PC |
Temperature rise | 0 ~ 40K |
Item | Capability of Test | Test Equipment | Reference Standard | Type of Test | ||
Factory Examination | Type Test | Reliability Testing | ||||
Appearance | Yes | Non | / | * | ||
Product Size | Yes | 2.5D Optical Instrument | / | * | * | |
Insulation Resistance | Yes | Insulating Dielectric Strength Tester | GB/T 24343-2009 6 | * | * | |
Dielectric Strength | Yes | Insulating Dielectric Strength Tester | GB/T 24344-2009 5.4 | * | * | |
Partial Discharge | Yes | Partial Discharge Tester | GB/T 16935.1-2008 | * | * | |
Temperature Rise Test | Yes | Programmable Frequency Converter | / | * | * | |
Distributed Inductance Test | Yes | Inductance Detector | / | * | ||
Distributed Capacitance Test | Yes | Digital Electrical Bridge | / | * | ||
Fastness Test | Yes | Electronic Universal Testing Machine | / | * | ||
Torsion Test | Yes | Torque Wrench | / | * | ||
Combustion Test | Outsourcing Test | UL 94 | * | |||
Low Temperature Test | Yes | Constant Temperature and Moisture Test Chamber | GB2423.01 2001 | * | ||
High-temperature Test | Yes | Constant Temperature and Moisture Test Chamber | GB2423.02 2001 | * | ||
Damp Heat Test | Yes | Constant Temperature and Moisture Test Chamber | GB2423.3 2006 | * | ||
High-low Temperature Cycling Test | Yes | Constant Temperature and Moisture Test Chamber | GB2423 | * | ||
Salt Spray Test | Yes | Salt Spray Test Chamber | GB2423.18-2000 | * | ||
Peel Strength Test | Outsourcing Test | / | GB/T 2790-1995 | * |
Selection of Insulation Materials
The low inductance of the laminated busbar could be ensured by using excellent insulating materials. In order to meet a series of requirements for the electric insulation or environment, customer could make an optimal option on the basis of actual application environment.
Material and Performance | Density (g/cm³ ) |
Thermal Expansion Coefficient |
Thermal Conductivity W/(kg.K) |
Permittivity (f=60Hz) |
Dielectric Strength (kV/mm) |
Flammability Rating |
Continuous Use Temperature |
Water Absorption (%)/24h |
NOMEX | 0.8~1.1 | 0.143 | 1.6 | 9 | 94 V-0 | 220 | ||
Polyimide |
1.42 | 20 | 0.094 | 3.5 | 9 | 94 V-0 | 220 | 0.24 |
Polyvinyl Fluoride |
1.38 | 53 | 0.126 | 10.4 | 19.7 | 94 V-0 | 105 | 0 |
Polyester Film |
1.38~1.41 | 60 | 0.128 | 3.3 | 25.6 | 94 V-0 | 120 | 0.1~0.2 |
NOMEX | Polyvinyl Fluoride | Polyester Film | Polyimide |
Excellent fire resistance and heat resistance; good chemical resistance; Favorable Mechanical Performance; Radiation resistance |
Excellent electrical performance and steady chemical property; Low hygroscopicity and flame resistance. |
Good electrical performance and chemical corrosion resistance; Low hygroscopicity and economical price. |
Favorable heat resistance, excellent electrical performance; Radiation resistance and flame resistance. |
Simulation Picture of the Laminated Busbar
Traditional Copper Bar Current Distribution Ls=73.4nH
Bus Bar Current Distribution Ls=10.6nH
Relationship between the Inductance of the Busbar and the Thickness of the Layer Insulation Material of the Busbar
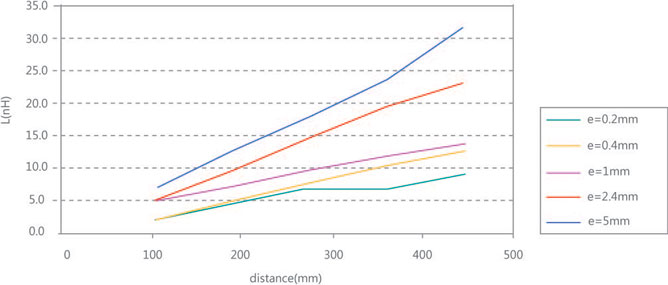
Power Electronics | Industrial inverter, inverters, wind power, UPS systems high density power distribution cabinets, electric welding machines, test equipment, large server and medical equipment |
Transportation | Electric locomotives, Railway trains, electromobile Electrically driven ships |
Aerospace and space | Satellite systems, Airliner, Space Shuttle, Missile systems |
Military | Submarines, Communication systems, Armored vehicles Radar systems |
Communication | IT servers, super computers |
Connection | Advantage | Disadvantage | Cost | |
Embossing | ![]() |
Good performance, high reliability | Technological limitations | Low |
Riveted bronze columns | ![]() |
Easy to make and it can meet all kinds of design requirements | Moderate mechanical performance, it is not suitable for harsh working conditions | Moderate |
Tin-brazed copper columns | ![]() |
Good mechanical performance, wide application range | / | High |
Silver-brazed copper columns | Compared with tin-brazing, it has lower resistance and higher temperature resistance | High cost | Higher |
Solution | Advantage | Disadvantage | Cost |
Slot | Easy to make, moderate cushioning effect | Lower electric performance | Low |
Local terminal heat treatment | Easy to make, good cushioning performance | If contact area is large, contact resistance will be increased and electrical performance will be decreased | Moderate |
Copper woven belt connection | Good cushioning performance, the assembly deviation has compensated | The terminal is longer and the stray inductance has increased | High |
Soft joint with copper foil | Good cushioning performance, the assembly unidirectional deviation has compensated | The terminal is longer and the stray inductance has increased | Highest |